
- #Galvanized steel stress corrosion cracking mechanism cracked
- #Galvanized steel stress corrosion cracking mechanism iso
One possible exception to this statement is the weathering steels, in which small additions of copper, chromium, nickel, and / or phosphorus produce significant reductions in corrosion rate in certain environments. Unfortunately, these levels of addition do not generally produce any remarkable changes in general corrosion behaviour. In carbon steel, the typical corrosion process can be regarded as the thermodynamically favoured reverse reaction of the metal-winning (extraction) process as shown in Fig 1.įig 1 Chemical reaction of iron during corrosion and metal extraction reactionĬarbon steel (which include mild steels) is by its nature has limited alloy content, usually less than 2 % by weight for the total of all additions. Since the carbon steels represent the largest single class of alloys in use, both in terms of tonnage and total cost, the corrosion of carbon steels is a problem of enormous practical importance. The cost of corrosion of carbon steel to the total economy is very high. It has relatively limited corrosion resistance. Metallic corrosion occurs since in many environments, the majority metals are not inherently stable and tend to revert to some more stable combination of which the metallic ores as found in nature are familiar examplesĬarbon steel is the most widely used engineering material. The metal being corroded forms the anode while the cathode is that being electroplated. Most simply stated, metallic corrosion is the reverse of electroplating. This can range simply from visual impairment to complete failure of technical systems which cause big economic damage and even present a hazard to the people.Ĭorrosion can be defined broadly as the destruction or deterioration of metal by direct chemical and electro-chemical reaction with its environment. Corrosion is seen when there is a change in the metal’s or system’s properties which can lead to an undesirable outcome.
#Galvanized steel stress corrosion cracking mechanism iso
#Galvanized steel stress corrosion cracking mechanism cracked
A model for crystallographic cleavage combining the stress component normal to the basal plane and the amount of plastic slip on the basal slip systems is proposed and identified from equibiaxial tension tests and electron backscattered diffraction (EBSD) analysis of the cracked grains. Grain refinement by recrystallization is shown to lead to an improved cracking resistance of the coating.
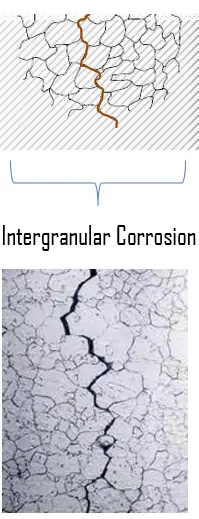
An extensive quantitative analysis based on systematic image analysis provides the number and cumulative length of cleavage cracks at different strain levels for the three investigated microstructures and three loading conditions. A complex network of cleavage cracks and their interaction with deformation twinning is shown to develop in the material. No fracture at the interface between the steel and zinc coating was observed that could lead to spalling, in the studied zinc alloy. Two main fracture mechanisms, namely, intergranular cracking and transgranular cleavage fracture, were identified in an untempered cold-rolled coating, a tempered cold-rolled coating, and a recrystallized coating. Plastic-deformation mechanisms are addressed in the companion article. The objective of the present article is to investigate the damage modes at work in three different microstructures of a zinc coating on an interstitial-free steel substrate under tension, planestrain tension, and expansion loading. Zinc-based coatings are widely used for protection against corrosion of steel-sheet products in the automotive industry.
